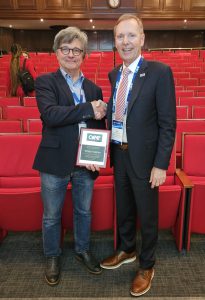
With Bill Kent of the Association of Energy Engineers after being presented with their Lifetime Achievement Award. In my acceptance speech I acknowledged just a few of the many people to whom I owe a debt of gratitude for the advice and inspiration they have given me over the years.
I’d start with Mike Horsley, a lecturer at Portsmouth Polytechnic (as it then was) and chairman of one of committees which I was responsible for servicing during my time as education officer and deputy secretary at the Institute of Energy (as it then was) in 1979-81. Mike encouraged me to render myself unemployed so that I could enrol on his 5-month full-time energy supervisors’ course, which in turn opened the door to my first job as an energy manager at Lambeth Council.
Colin Ashford was my opposite number at Hackney Borough Council and an enthusiast for personal computers, which in those days were almost unknown in the workplace. Colin invited me over to see how desktop computers could be applied to energy management, and convinced me to get one at Lambeth (where I think for a while I may have been the only person using one).
From there I moved across to Gloucestershire County Council to work with Mike Simpson, a highly experienced and competent energy manager who helped me enormously in developing my craft, and John Willoughby, our colleague who was energy manager for the local technical college campuses. John was not only an expert in energy saving in buildings (and incidentally the founding editor of Energy in Buildings magazine) but also a former lecturer who got me interested in training. It was John’s example that led to my use of models and physical aids on training courses.
While I was at Gloucestershire I had a phone call from Andrew Buckley, in more recent times director of the Major Energy Users’ Council but in those days the owner of a publishing and training business specialising in energy subjects. I’d originally encountered Andrew in my Institute of Energy days when his company had published the Directory of Qualified Energy Consultants which I had developed as an in-house reference document. Now, however, he became animated when I said I was applying desktop computers to energy management. He asked if I could do a book on the subject (which I did) and run some training courses for him… Which I did, after resigning from my job and going to my bank for a loan (£15,000 in today’s money) to buy ten computers.
Andrew had meanwhile introduced me to his colleague Dr Peter Harris who was presenting training courses on energy monitoring and targeting. It was Peter who introduced me to degree-days and cusum analysis, which completely transformed the way I went about analysing and managing energy, and became the foundation of what I subsequently did as a self-employed energy consultant. Combining the analysis techniques with the newly-emerging personal computer got me into selling energy monitoring and targeting software and providing expert advice in that domain.
For a while in the mid-1990s my brother-in-law Joe O’Keefe worked with me as a (somewhat older than average) intern because he wanted a radical change of career path. Not having much to employ him on, I gave him free rein to tinker with computers and it’s thanks to Joe that the vesma.com website appeared in 1996… The perfect gift for an ardent self-publicist like me.
Sadly some mis-steps ensued and just short of my tenth anniversary as a self-employed consultant I came close to going bust. Luckily I was rescued by Roger Hawes who was running the energy team at Torpy and Partners in Bristol and took me on when I asked for a job, something I will always be grateful for. Likewise John Mulholland who persuaded NIFES to take me on after Torpy’s became part of the Enron empire (I bailed out because I thought Enron’s European business was doomed to fail; I did not suspect the true scale of the looming disaster). John ran NIFES’s training division and was another person who helped me hone my training skills. He looked after his team exceptionally well and I remember he always had my back with the directors when I overstepped the mark.
In due course, and prompted by the financial crash of 2008/9, I left John’s team to strike out on my own once more; and while looking for collaborators and associates I renewed my acquaintance with Andrew West, who lives a few miles away and had helped me with monitoring and targeting projects in the 1990s. In the intervening years Andy had changed his career path radically and become a book-keeper. To cut a long story short he agreed to come on board and take care of not just book-keeping but other administrative tasks. It’s fair to say the business was never more successful than when Andy was there to deal with back-office distractions.
The provision of free degree-day statistics has been a cornerstone of my marketing for 35 years so it would be churlish not to acknowledge the help I got from The Thatcher Government in 1991 when they discontinued the supply of official degree-day data. It created a vacuum that I was able to fill with prominent monthly exposure in the print media, and ultimately even became a source of revenue when they were shamed into reinstating it and found that they weren’t allowed to accept a single tender from the Met.Office. But that’s a different story.
The full list of those who’ve helped me along the way would be long and in some cases complicated to explain. So with apologies to those that I haven’t mentioned I would just like to thank my loyal clients over the years and all the bulletin readers who sent in the awkward technical questions on which subsequent issues were based.