In the UK when estimating fleet energy consumption from vehicle mileages, we may choose to use the tables published in official guidance (extract illustrated below) which convert distances in miles or kilometres to kWh consumptions for different classes of vehicle.
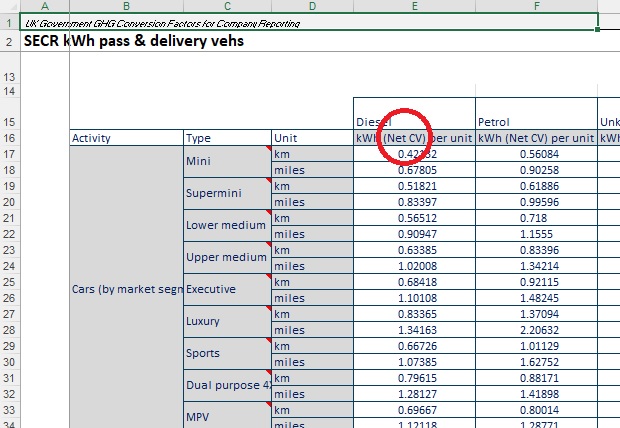
As indicated in Figure 1, the conversion factors are stated on a net calorific value (NCV) basis. However, this is not compatible with the way we normally account for energy in the UK. We actually use gross calorific values (natural gas, which of course is our predominant fuel for static applications, is billed on a GCV basis). For consistency we should account for transport fuels on a GCV basis as well.
What difference does it make? A fuel’s gross calorific value is a measure of its total energy content, whereas NCV ignores that fraction of energy which will be lost as latent heat in water vapour in the exhaust. The higher the hydrogen content of a fuel, the greater the discrepancy. Forecourt diesel’s GCV is 6.3% higher than its NCV; for natural gas the difference is 10.8%.
To convert kWh quantities based on NCV to their GCV equivalent you need to multiply by the following factors:
Aviation Spirit 1.053
Aviation Turbine Fuel 1.053
Burning Oil 1.053
Butane 1.084
Coal (domestic) 1.053
Coal (electricity generation) 1.053
Coal (electricity generation – home produced coal only) 1.053
Coal (industrial) 1.053
Coking Coal 1.053
Diesel (100% mineral diesel) 1.064
Diesel (average biofuel blend) 1.063
Fuel Oil 1.064
Gas Oil 1.064
Lubricants 1.064
LPG 1.074
Naphtha 1.053
Natural Gas 1.108
Natural Gas (100% mineral blend) 1.108
Other petroleum gas 1.087
Petroleum coke 1.053
Petrol (100% mineral petrol) 1.053
Petrol (average biofuel blend) 1.055
Propane 1.086
Waste oils 1.071